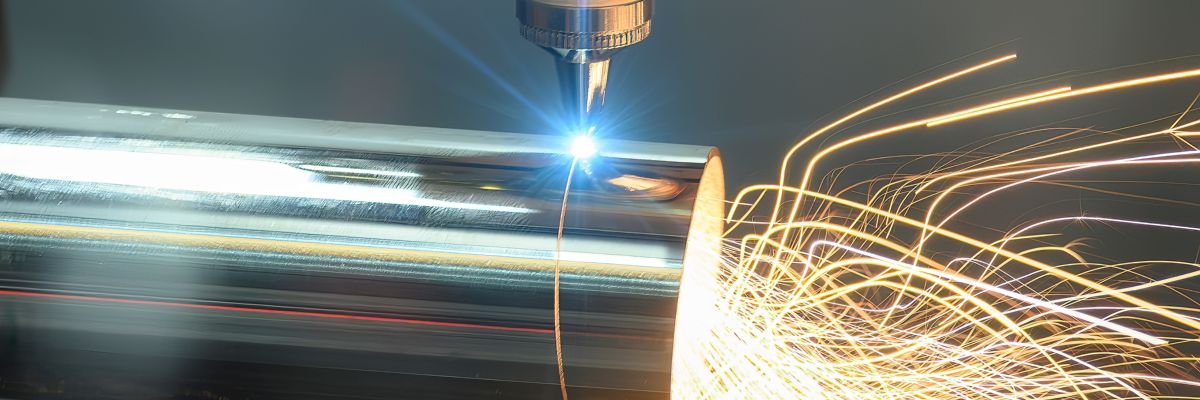
Laser micromachining: inspired by sharks
04. 11. 2024
Bacteria-resistant shark scales, sticky gecko feet, or lotus leaves that repel water – nature designs ingenious surfaces. But can we replicate them? Read our second feature on light, first published in the 3/2024 (Czech) issue of A / Magazine, below.
Catheters are essential for patient care, drug delivery, and drainage of bodily fluids, but prolonged use can lead to dangerous infections, with life-threatening bacteria appearing on their surface. That’s why researchers are exploring ways to modify or improve the materials used in such medical devices, often drawing inspiration from nature. Surprisingly, light – specifically, lasers – plays a key role.
Shark skin, with its rough scales, is naturally resistant to bacteria. Its surface has structures shaped in a way that cause foreign substances to slide off. If bacteria do manage to adhere, their cells bend between sharp ridges or are pierced and killed. Similar sophisticated surfaces are found on cicada wings and those of other insects.
And then we have lotus leaves with their water-repellent surfaces, snake skin that minimizes friction, and gecko feet that can cling to almost any surface. But how can we replicate these natural marvels and create micro- or nanoscale superstructures?
Lasers as precision tools
Material surfaces are conventionally modified through machining – a process of shaving off or removing fragments to achieve the desired shape. Traditional machining tools include saws and scrapers, while more advanced methods use lathes and milling machines. For micro- and nanoscale work, lasers are the perfect tool.
Current techniques typically use a single laser beam, which moves across the surface using motorized mirrors or sliding tables. However, processing fine details on the microscale is extremely time-consuming. This slowness, along with high costs, explains why “shark skin” or “lotus leaf” surfaces aren’t being mass-produced yet.
To put it in perspective, creating one square centimeter of water-repellent surface with a high-powered laser would take about one minute. Producing one square meter would thus take seven days. “For industry purposes, this speed is utterly unprofitable. We’re working on ways to make laser machining faster and more efficient and to transfer our findings from the lab into the real world,” explains Petr Hauschwitz, leader of the laser micromachining team at the HiLASE Center, which is part of the Institute of Physics of the Czech Academy of Sciences (CAS).
Ing. PETR HAUSCHWITZ, Ph.D., MBA Petr Hauschwitz studied laser technologies and physical engineering at the Czech Technical University in Prague. His dissertation on ‘large-area functionalization of surfaces using laser-created micro- and nanostructures’ earned him first place in the category of Best Doctoral Thesis at the Werner von Siemens Awards in 2022. In 2023, he received the Otto Wichterle Award, awarded by the CAS to young, talented scientists. He has worked at the HiLASE Center since his studies, leading a research group there since 2019. Together with his team, he holds two world records in productivity and the number of laser beams used in nanomachining (both from 2021). |
Light-speed innovation
During his doctoral research, Hauschwitz focused on designing superhydrophobic (water-repellent) surfaces. He drew inspiration from the lotus leaf, which is covered with nanostructures that give it remarkable properties, like self-cleaning: water droplets form spherical shapes and roll off the leaf, carrying away dirt and dust. This phenomenon is known as the “lotus effect.”
A cleaner leaf is better protected from algae, bacteria, and fungi, reducing the risk of disease while improving access to sunlight, thus enhancing photosynthesis. The technology to produce such surfaces has been known for some time, but Hauschwitz’s goal was to simplify and speed up the process.
The researcher experimented with different methods of making production more efficient. The breakthrough came with parallelization – splitting one laser beam into multiple functional parts. In his dissertation, he demonstrated that it is possible to machine surfaces using over 700 laser beams simultaneously. His innovative approach caught the attention of the Werner von Siemens Award jury, which awarded him the prize for best dissertation in 2022. A year later, he received the Otto Wichterle Award from the CAS that recognizes talented researchers under 35.
HOW TO SPLIT A LASER BEAM Creating 1 cm² of functional structure with a single laser beam would take one minute. To produce 1 m² would require 7 days. To speed up the process, Petr Hauschwitz’s team uses three main methods, selected based on the specific application: DIFFRACTION BEAM SPLITTING The beam is split by a pre-designed diffraction grating. Its simplicity is an advantage –the grating is just placed into the optical setup. It can withstand very intense laser beams, but it is expensive. Designing and manufacturing a grating costs around 10,000 to 20,000 EUR. Reproducing the element is about five times cheaper. INTERFERENCE STRUCTURING Similar to diffraction, but more flexible. By changing the angle at which beams intersect, the period of the interference pattern (the distance or size of individual points) can be adjusted. This method can bypass the diffraction limit of the optical lens and create structures smaller than the wavelength of the laser beam. DYNAMIC BEAM SHAPING This method allows real-time shaping and splitting of beams using a liquid-crystal spatial light modulator. By rotating the crystals, the wavefront of the input device changes, shaping the beam. While flexible, liquid crystals cannot handle high laser energy or power. |
Machining at the nanoscale
Under a microscope, shark scales resemble a neatly arranged grid of grooved rectangular tiles, while the surface of a lotus leaf, covered in tiny protrusions, looks like a volcanoscape. The microstructure of gecko feet resembles a shaggy carpet with frayed tips, and snake skin consists of dense clusters of sharp micro-spikes.
To replicate these surfaces, one must first create a 3D computer model or grid of the desired structure. This model is then used to program a laser machining tool, which uses beams of light to remove tiny fragments from the material, layer by layer.
A prototype of a strain sensor, used in fields like robotics. It is the result of extremely precise micromachining, where the laser had to evaporate a layer just 250 nanometers thick without damaging the underlying ceramic layer.
Unlike traditional machining, which generates a significant amount of waste, laser micromachining produces minimal waste – often in the range of mere micrometers. The removed material either melts or, more commonly, vaporizes. Since the process occurs on a microscopic scale, to the naked eye, the finished product might appear identical to the raw material. The difference, however, is detectable under a microscope or when a precise weighing scale is used.
Despite the high precision involved, functional surface machining doesn’t require a massive laboratory. The lab at HiLASE, for example, is comparable in size to a small bedroom. Even the machining equipment is surprisingly compact. At its core is a laser, in this case the PERLA laser, developed in-house by the scientists and engineers at HiLASE. It boasts an exceptionally high beam quality and high pulse energy, enabling the parallelization of production across multiple beams.
PROJECT LASAPP The development of antibacterial surfaces, a collaboration between the laser micromachining lab and the Faculty of Science at Charles University’s BIOCEV Center, is now supported by the interdisciplinary LasApp project. “We’ll be developing functional bacteria-resistant surfaces, while Zdena Palková’s team at BIOCEV will study how microbes react to these surfaces,” Petr Hauschwitz explains. LasApp builds on the recently completed Strategy AV21 program, Light in the Service of Society. It involves institutions with a history of developing the first Czechoslovak lasers in 1962–1963. The project is coordinated by the Institute of Photonics and Electronics of the CAS, a leader in fiber laser development in the Czech Republic. The main goal of the project, which stood out among 66 others in the Excellent Research call of the Johannes Amos Comenius Operational Program, is to advance both fiber and thin-disk laser technologies. Its application potential spans beyond medicine into aerospace and defense industries. |
Speed and efficiency in production, however, don’t depend on the laser’s power alone. The key is to skillfully split the laser beam so it can work on multiple areas simultaneously. Hauschwitz’s team has already broken several world records in this regard. “Our current record is over 40,000 beams working simultaneously. We’ve reduced the time needed to machine one square meter from seven days to just five minutes, and we are now able to structure details smaller than a micron,” the researcher says.
To be precise, 40,401 laser beams were used in parallel to machine a single material. The project involved creating a superhydrophobic surface resistant to ice, corrosion, and air resistance – perfect for use on aircraft wings. This level of beam division was achieved using a special diffraction grating, custom-made for the HiLASE team by the Israeli company HOLO/OR.
From space to microbes
The breakthrough in laser beam-splitting technology and the dramatic acceleration in producing superfunctional surfaces has caught the attention of industry leaders and innovative startups alike. The HiLASE team is making a name for itself, and exciting collab opportunities are emerging. Recently, a Canadian company approached the team to create a superhydrophobic surface for a 650 × 300 mm metal sheet for use in cooling systems. The company had been unable to find anyone in North America capable of doing so.
The unique methods developed by Czech researchers are also being applied in space technology. One of their successful projects involved drilling micrometer-sized holes in graphite and ceramics for use in satellite engines. Hauschwitz has also highlighted strong partnerships with local innovative companies like IQS, which manufactures holograms for ID cards, among other products. In a joint project currently in development, they are working on creating antimicrobial catheters and other medical devices at high risk of bacterial infection. These are often long, closed-off tubes, and forming a controlled functional nanostructure on their inner surfaces is particularly challenging. “We’ve figured out a way to do it, and if we succeed, we could be the first in the world to master this technique,” Hauschwitz adds.
LIGHT HARNESSED IN A LASER A laser is amplified light concentrated into a highly powerful beam. The principles behind how it works were described by Albert Einstein in 1917, and the first laser was built by American physicist Theodore Harold Maiman in 1960. Over time, lasers have been continually improved, with a major breakthrough occurring in the 1980s when Donna Strickland and Gérard Mourou developed the technique of chirped pulse amplification, for which they received the 2018 Nobel Prize in Physics. This method enabled the creation of large laser systems around the world with top-tier performance. One such facility is Hauschwitz’s home institution in Dolní Břežany, Czech Republic. Lasers at HiLASE generate extremely short pulses, sometimes in the femtosecond range (about 10⁻1⁵ seconds). While this high-energy output makes extraordinary feats possible, it also poses a risk of damaging both the material being processed and the laser equipment itself. That’s why researchers have developed various techniques of “taming” these high-energy beams. As a result, HiLASE has set several world records for laser performance. Read more about HiLASE’s milestones here. |
Antimicrobial surfaces, inspired in part by the unique scales of sharks, could also find use in materials for joint replacements, a project Hauschwitz’s team is hoping to pursue in collaboration with the Czech company Prospon. Another HiLASE group, specializing in laser shock peening, will be involved in this project. Their methods can extend the lifespan of highly stressed components, which is especially desirable for joint implants.
Laser micromachining has proven to be valuable in medicine, industry, and space. Czech researchers are determined to be trailblazers in this field. When asked about his goals for the coming years, Hauschwitz doesn’t hesitate. “When anyone in the world asks about the best micromachining labs, I want ours to be at least among the top five contenders.”
The PERLA laser, developed at HiLASE, is used for laser micromachining. It generates a high-quality beam (1,030 nanometers, 970 femtoseconds, 100 watts), which researchers split to maximize efficiency.
Written and prepared by: Leona Matušková, External Relations Division, CAO of the CAS
Translated by: Tereza Novická, External Relations Division, CAO of the CAS
Photo: Jana Plavec, External Relations Division, CAO of the CAS; Shutterstock
The text and photos are released for use under the Creative Commons license.
Read also
- A trapped state: The pandemic impact on public attitudes, trust, and behavior
- Aerial archaeology: Tracing the footsteps of our ancestors from the sky
- Archaeologists uncover ancient finds along Prague Ring Road
- Our microbiome largely depends on what we eat, says microbiologist Michal Kraus
- The ABCs of writing: Why did its invention mark a turning point for humankind?
- We learn, remember, forget… What can memory actually do? And can we outsmart it?
- New Center for Electron Microscopy in Brno opens its doors to global science
- The hidden lives of waste: What can we learn from waste workers and pickers?
- A unique lab is hidden right beneath Prague’s Vítkov Hill
- Renewables are a strategic investment in European security, scientists say
The Czech Academy of Sciences (the CAS)
The mission of the CAS
The primary mission of the CAS is to conduct research in a broad spectrum of natural, technical and social sciences as well as humanities. This research aims to advance progress of scientific knowledge at the international level, considering, however, the specific needs of the Czech society and the national culture.
President of the CAS
Prof. Eva Zažímalová has started her second term of office in May 2021. She is a respected scientist, and a Professor of Plant Anatomy and Physiology.
She is also a part of GCSA of the EU.